- Dongguan Dow Nano Chemical Co., Ltd.'s specifications for the use of Polypropylene yarn pre-spinning oil!
- The suspension of tariffs once again has significantly alleviated the cost pressure on enterprises
- The advantages of TAO NANO Polypropylene yarn spinning oil are prominent. Let's take a look together
- Advantages of Polypropylene yarn spinning oil
- How to use the polypropylene precursor oil of TAO NANO CHEMICALS(DONGGUAN) CO.,LTD.?
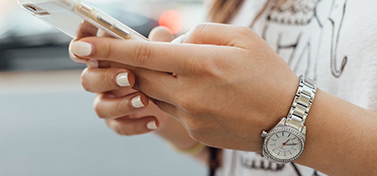
- Contact: Miss Tang
- Telephone: 0086-18926870629
- Email: taonano@taonanooil.com
- Address:No. 59, Liantang Road, Sanzhong Village, Qingxi Town, Dongguan City, Guangdong Province
Polypropylene yarn spinning oil is an indispensable special auxiliary agent in the production process of polypropylene fiber, which plays a decisive role in the processing performance of the fiber and the quality of the final product. Polypropylene fiber is made of polypropylene, and the molecular structure lacks polar groups, which leads to poor hygroscopicity, weak conductivity, and high friction coefficient. It is easy to have problems such as hair, broken ends, and static electricity accumulation during spinning and subsequent processing. Polypropylene yarn spinning oil effectively solves these problems by forming a uniform oil film on the fiber surface.
Core function analysis
Balance between smoothness and clustering
The smoothing agent (such as fatty acid esters) in the Polypropylene yarn spinning oil can reduce the dynamic friction coefficient between the fiber and the metal, and between the fiber, and reduce the processing resistance; the clustering agent increases the static friction coefficient, enhances the fiber cohesion, and prevents the loosening of the bundle. For example, when winding at high speed (>800m/min), the oil needs to take into account low viscosity and high clustering to avoid oil droplets splashing or bundle breakage.
Antistatic performance optimization
The insulation of polypropylene makes it easy to generate static electricity, which causes the fibers to wrap around the equipment or repel each other. Antistatic agents (such as fatty alcohol phosphates) added to the oil form a conductive layer by absorbing moisture in the air, significantly reducing surface resistance. Amphoteric surfactants can still maintain antistatic effects in low-humidity environments, but the byproduct sodium chloride content needs to be controlled to prevent metal corrosion.
Heat resistance and stability guarantee
During the hot stretching process (170-220℃), the Polypropylene yarn spinning oil must have a high boiling point and low volatility to avoid high-temperature coking or fiber yellowing. Some formulas introduce mineral oil or polyoxyethylene ether ingredients to enhance the strength of the oil film and ensure that the fiber can still maintain uniform stretching at high temperatures.
- Dongguan Dow Nano Chemical Co., Ltd.'s specifications for the use of Polypropylene yarn pr
- The suspension of tariffs once again has significantly alleviated the cost pressure on ent
- The advantages of TAO NANO Polypropylene yarn spinning oil are prominent. Let's take a loo
- Advantages of Polypropylene yarn spinning oil
- How to use the polypropylene precursor oil of TAO NANO CHEMICALS(DONGGUAN) CO.,LTD.?